As expected, the windows are being set in the window frames. Right now, they're squaring and securing them in the bucks, but not insulating them because the trim carpenters will get a chance to look at how they're going to install the window trim and siding before everything is sealed in. Mike found that two of the windows, one of the arched tops for the side of the great room, and the smaller arch top on the laundry room, were damaged during transit and contacted Pro Brothers. They're already rush ordering replacements for those two windows. The laundry room window isn't going in right away to provide second floor access for the dry wall, but the great room window will create some difficulty. Those windows will need to be placed with a lift, so we'll need to get the lift two times. Security won't be an issue since the opening is 30 feet up.
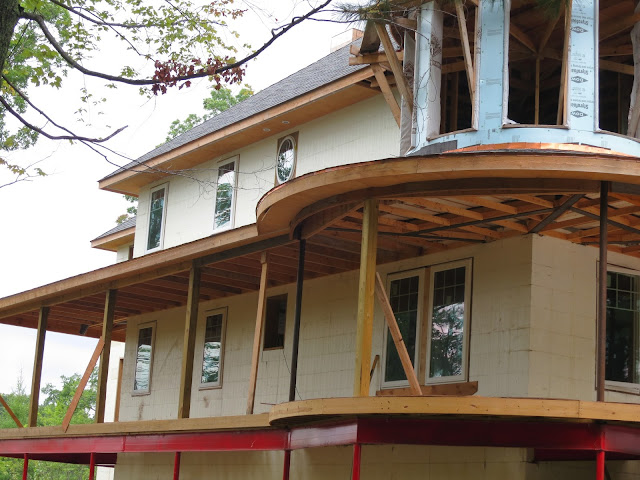
Most of the windows on the side of the house have been installed. The turret windows will need some extra consideration since the turret roof comes down on the window opening so low. Originally, we wanted to put some dentil molding up there, but that doesn't look like it will be a possibility. Now we're looking at corbels in between the windows; just trying to capture a bit of that Victorian look without making it too gingerbread.
You can see the round window opening is prepped for installation and the study windows are already in. We went with the 1/3 window grid rather than having half the window obscured with mulls so we could get a better view outside. When we visited the site on Saturday, they were still there installing the windows for a few more hours so they probably got the round window set already. I don't think they could have finished it up, especially considering the great room windows, but they'll probably get it done this week.
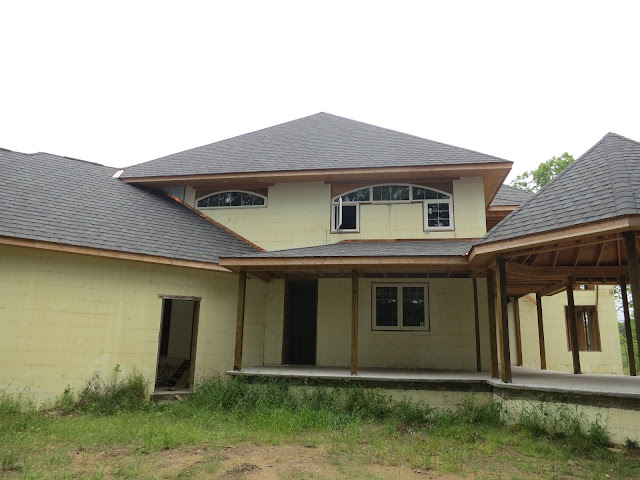
All the master bedroom windows have been installed and you can see the bedroom and bathroom windows here. Also the kitchen window was in place, so it was nice to open it and take a peek at what our view of the back yard would be like. The master bedroom window is on the left and has two opening elements, just to each side of the bed. The bed will sit under the arch window and two night stands will sit under the side windows. We couldn't get all the mullion grids on the master bedroom eyebrow and lower windows to line up but that's okay. I would rather have evenly spaced mulls in their respective frames and the offset isn't too great.The other arch eyebrow window is in the shower and is the sole light providing window for the master bathroom. There will be a long bench under that window in the shower so it will be possible to look out when standing on the bench. Unless you're on the roof, you would be hard pressed to be able to look in so it will be nice to have light with privacy.
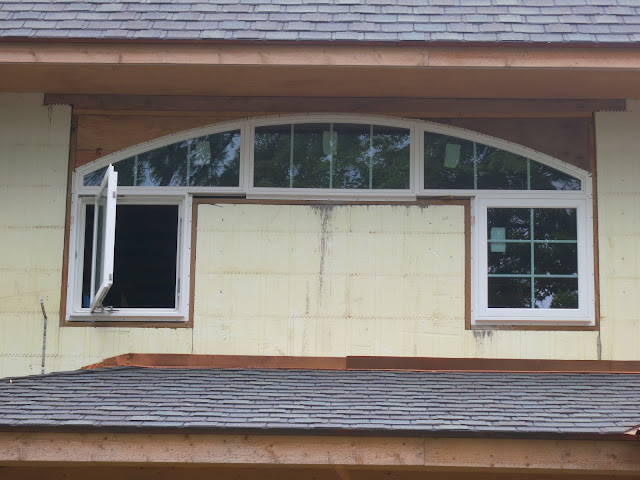
A little closer look at the master bedroom windows. This eyebrow came in three sections that were assembled during installation. You can see the nailing flange on the center section compared to the missing nailing flange on the side pieces, since they meet up with the lower windows. There are mull installation spacers that install between the sections and fill the gaps. Obviously once the window trim is in place, you won't see any gaps around the windows. Those will also be filled with insulation, most likely spray expanding foam. All the nailing flanges will be flashed with a self adhesive membrane which will then be covered by the window trim and siding. We were debating if we needed a membrane in the window opening as required by standard construction houses. Since the bucks are all pressure treated wood, we're not worried about the rare occasion when water could penetrate to it. Also, since the wood shingle siding is already spaced away from the ICF, there's no threat to water infiltration staying behind the siding and rotting it out from behind.
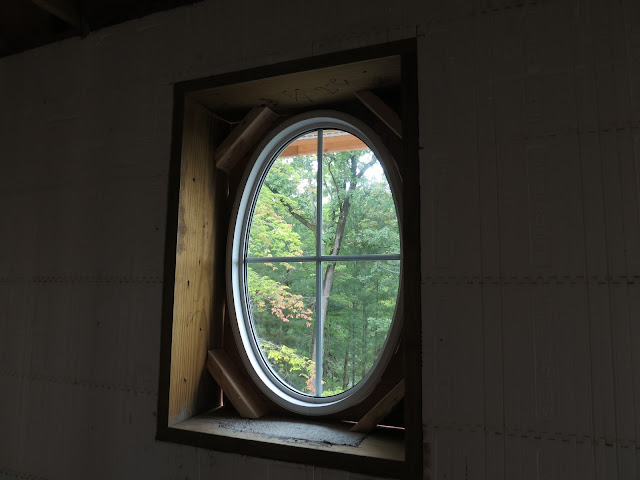
Here's how you fit a round (or oval) window into a square opening. The corners are bucked out and a plywood mask is applied through which the window can come through. I guess this inside of this window might be a little weird depending on how we finish it. The easiest way to finish it would be to keep the rectangular box and finish the sill as such, filling out the space around the oval window. I think the best way would be to some how bring the whole oval forward to the interior wall depth so the opening remains oval. I'll have to ask Mike about this but I think the latter method is preferred.
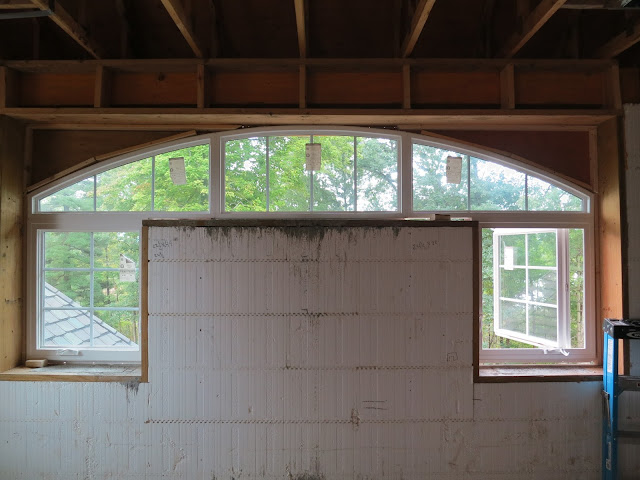
Here's the inside of the master bedroom window. Besides this, there's another window on the left wall, as well as the french door to the balcony so I don't think we'll be short on natural light. We're actually considering how to install light blocking since sleeping times could be during daylight hours. The space between the windows is perfect width for the California king bed we have right now so all smaller beds will also fit. I think two full sized beds are wider than a California king so if we want to full sized adjustable beds when we're super old, some of the beds will overlap the window space.
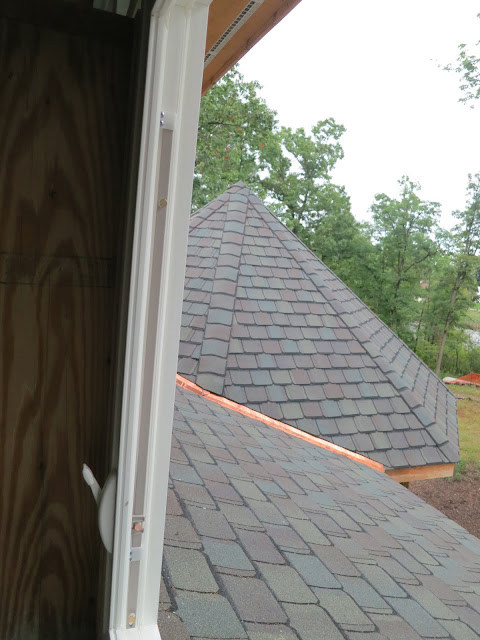
Here are some details on the windows and what makes them so appealing. Here's the locking mechanism for the casement window. Normally, you would see two latches and two locks. The locks aren't only for security, they also pull the window tight against the sash to create the air seal. The
Soft-lite design has one latch for ease of use, but it moves the entire bar to engage/disengage three locking points on the window frame. Since frames can flex, having more locking points is better to have an air tight seal. The sliding bar locking lugs are all metal and they're captured by high desity poly urethane brackets which self lubricate so they'll always operate smoothly.
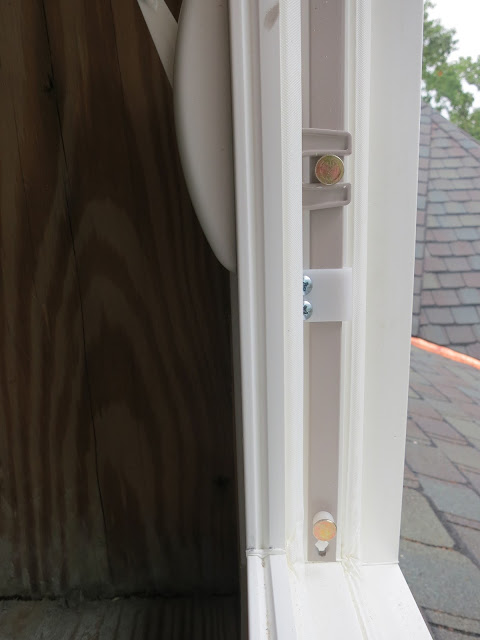
Here's a close up of the locking mechanism and lock bar. The locking mechanism engages the bar and the lock point simultaneously, and you can see the lower locking lug at the bottom. Should the HDPE bracket break, they'll be easy to replace and the simple design makes fabrication easy if I ever need to make my own. You can also see two of the three window seals in this picture. From left to right, there's one that partially obscures the HDPE bracket screws, and one just on the other side of the locking bar. The last window seal is on the casement itself and sits even farther out from these two seals. It's no wonder they can achieve a 0.02 cfm air infiltration with this set up.
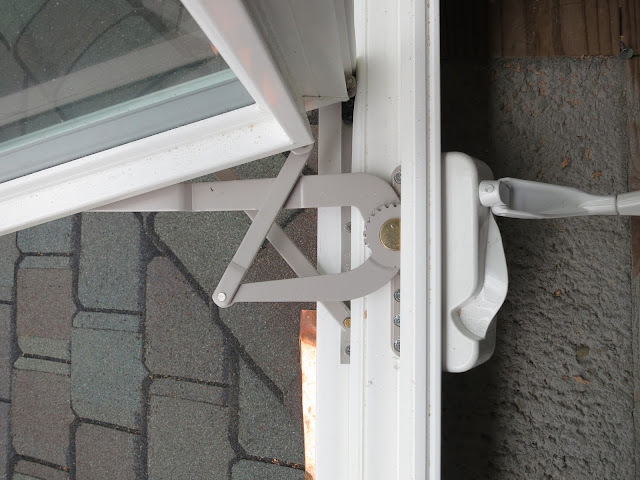
Here are the
Truth Encore dual arm operators that come with the Soft-Lite casements. I've heard that Truth makes some of the best hardware available and it's reassuring that parts will be easy to obtain if needed. The cranks are very smooth and require little effort to open and close the windows. The ratio of handle turning to window opening is a little low so it does take a good number of turns to open completely, but that's a small trade off for less resistance. As far as I can tell, to clean the exterior of the window, you just need to crank the window open to 90 degrees, and there's enough space between the sash and window to clean. It's a pretty simple operation, but almost all our windows are accessible by the wrap around porch anyways so it's a non-issue. Cleaning the exterior of the great room windows will be a trick. For closing, after the cranking to almost closed and engaging the window lock, it still takes a hard quarter turn of the crank to get it to the stowing position. It's an odd operation, but not that annoying.
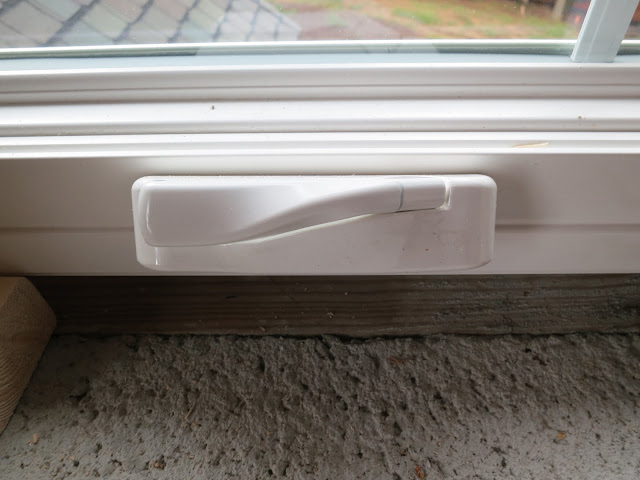
Here's the crank in the stored position. Nice and clean. As far as I can tell, all the parts are cast aluminum and the crank and case are easily removable if we wanted to paint them a different color. We'll be keeping them white. Another nice feature of an ICF house is having a huge window sill on the inside. Since the walls are ten inches thick plus drywall and the windows mount more towards the outside, there's a lot of sill space on the inside for window treatments or small potted plants. Margaret was happy when she learned how much space we'll have to hang window treatments.
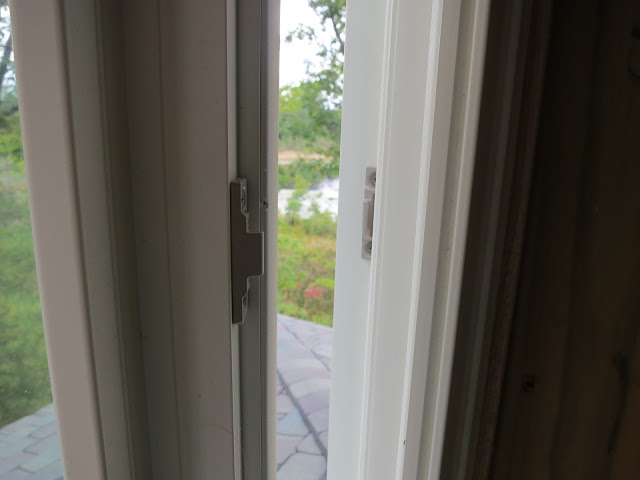
Another nice feature of the Soft-Lite windows is on the hinge side of the window. You'll find these locking lugs that engage when the window is closed so it doesn't only rely on the hinge strength for air tightness. The lugs engage each other as the window closes and creates another lever point to press the casement against the sash weather seals. That means positive locking pressure on both sides of the window. Very nice.
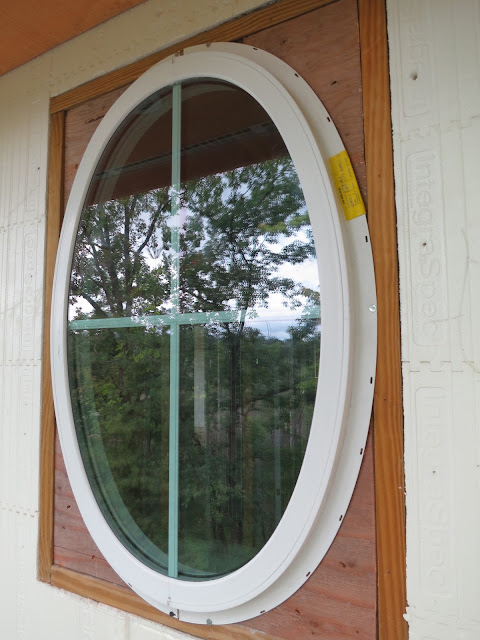
Here's what the exterior of the oval window looks like. You can see that not all the nailing flange is secured right now. They're just setting the windows for security and will come back to secure the entire flange before flashing and siding. There's enough there to securely hold the window in place. As with all windows, the mulls are internal so they're easy to clean. The window molding will have to be curved but this will be easy since we're not using any complicated profiles. Basically, it's not so much about curving wood, but cutting a curved piece from a wide piece of wood.
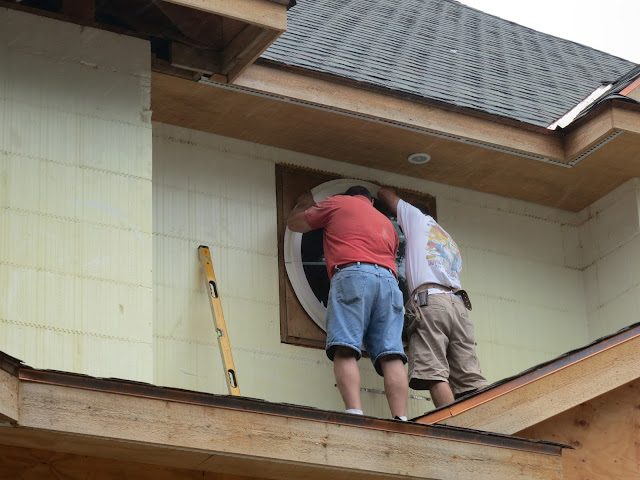
Here they are fitting the round window as we were leaving. We didn't get to see it in place since they needed to fine tune the fitment, but it's probably in place now. The guy in the salmon shirt is our builder, Mike. Every time a sub-contractor has been out there, he's been here. As you can see, he's not scared to get in there and help, and that's a refreshing change. We spoke for an hour, discussing all the things that will need to be "fixed" in order to get the house to a state where they can continue to build. Not too much with the inside of the house, a few places where the ICF buckled and will need to be smoothed. Some missing blocking in the roof. Most of the issue is with the porch and how it will interface with the stone and siding. Some areas of the porch roof will need to be bolstered. Little things that make me wonder how Matt and Ken were going to tackle them. For instance, the hidden room under the porch needs a concrete slab poured on it. Pouring a 2 inch slab will bring the height up to the level of the deck joists. Unfortunately, you have to consider how the deck boards will span this part. Since Azek uses hidden fasteners that usually attach to joists, was the plan to tap-con down into the concrete? It's not really okay for the Azek to be sitting right on the concrete, so a spacer would be desired. Maybe the slab could be poured to 1.25" thick and a 3/4" spacer tap-conned to the concrete as a nailer for the hidden fastener. Or maybe it's okay to put the Azek on concrete and just use adhesive between the two. Stuff like this will need to be figured out, but it seems like it could have been avoided if steps were taken in the design.
We also met with the California Closets designer to get preliminary measurements on the master closet, laundry room craft area, and pantry. We'll have a follow up meeting later this month to take a look at materials and initial organization design. Of course, a final measurement won't take place until all the drywall is in, but at least we can get the ball rolling on this process and plan for the cost.
Jonathon of
The Sound Vision also came out to meet with Mike, but I got a chance to catch up with him. He detailed his requirements for the electricians, and it seems like it will make their job easier, at least in the rooms that will have lighting control. Not much changed from the initial design, but some technology will be difference since advances were made. Looking forward to seeing that all implemented.
So that it for this week. Next week should have almost all the windows installed. After that the rough carpenters will come in to fix the various issues we need to fix before we can move forward. Mike should have all the subcontractor bids in this week so we can present our time table and budget to the bank. It will be interesting to see what the difference is between the last budget and this one. We pretty much knew the old numbers were under budgeted when we started pricing out cabinets, but we didn't have a feel how much the finishing work would cost. It will be nice to not have to pay so much out of pocket for every milestone. I have a meeting with Great Oaks later this week so we can all get on the same page about finishing up phase 1 and planning out the next phases. There's a lot going on even though the days are getting shorter.